First National Technical Center with latest state of the art patented equipment in cooperation with Cambridge Dynamics and Beckhoff New Automation Technology (PLC systems).
*Covering
a total area of 5,000 sq.m (or
50,000 sq.ft)
- This implemented technical center consists of Dynamic & Static testing
managed by a R&D team of 30 engineers.
*Total
investment > RMB 50 million.
*Core
strategic project.
*Fully
state-of-the-art patented design and equipment - Operated by the industry
experienced specialists.
*The
test center is fully insulated with air exchanges (environmentally friendly)
and consistent humidity and temperature (to provide best testing
conditions).
*The
test will be running on ASAE, DIN, ISO, RMA & SAE standard.
Testing Centre will have the following Rigs:
* 10-off 15kW Rigs
* 10-off 30kW Rigs
* 10-off 75kW Rigs
* 2-off 100kW Rigs
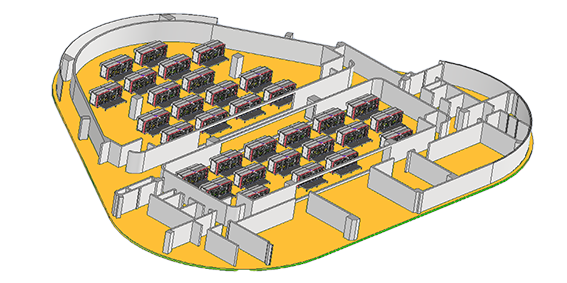
30kW Rig containing:
*DriveR Pulley.
*DriveN Pulley.
*6 off Idler Pulleys.
*A satellite unit can increase belt length capabilities, adding 5 more idler pulleys
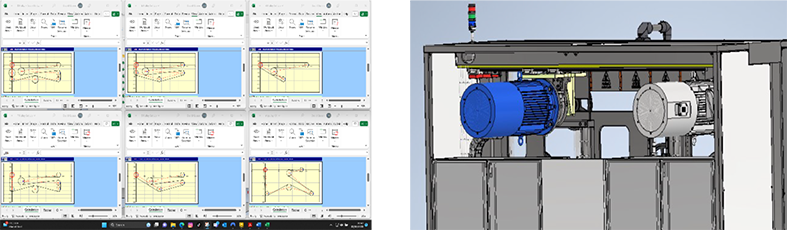
Department will have a fully inclusive IT system in control of:
*Test assignment.
*Product input.
*Pulley lifetime monitoring.
*Calibration.
*Real time data and photograph collection.
*Automated reporting (incl. identical testing of different manufacturers across multiple rigs).
*Authorized access is possible globally – Real time
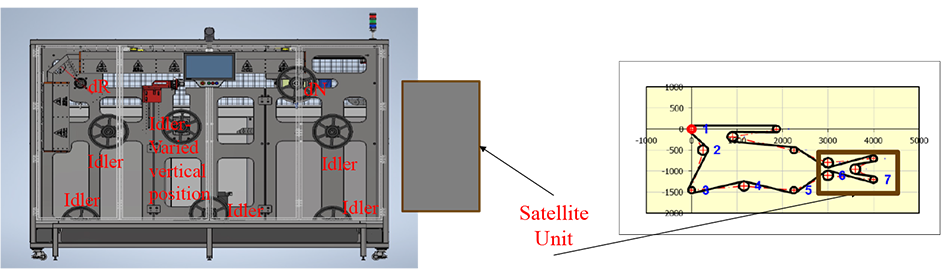
Rig advanced features are as follows:
*Ability to fit a large range of belt lengths (800mm to 16000mm) and types (Wrapped V-Belt, Cogged V-Belt, Ribbed Belt, Variable Speed Belt, Banded Belt, as well as Timing Belt).
*Belt life is greatly affected by temperature - our rig will capture life time behavior of:
- Working temperature changes due to friction.
- Belt life and performance under incremental temperature change.
- Slip on Driver pulley versus Driven pulley as slippage causes heat variations in the belt.
*Our rig will test and capture the physical changes of the belt under the following conditions:
- Effect of back bending on belt due to bending around back idlers.
- Wear of belt through dynamic micro photography.
- Dynamic tension loss.
- Real time belt measurement via infrared lasers.
- Early failure detection, vibration sensor paired with temperature change - facilitating better diagnosis of belt failure.
*Comparative testing (versus competition or others) through multiple rigs output from live reporting canl be linked on real time.
Data capture:
All data are saved for analysis using our integrated AI - Able to investigate and determine the root cause of failures and determine which of the belt elements will need improvements, updates, and/or changes. Able to further develop new generation programs based on our AI further data analysis and formulations.
Testing Centre will have the following Rigs:
* 10-off 15kW Rigs
* 10-off 30kW Rigs
* 10-off 75kW Rigs
* 2-off 100kW Rigs
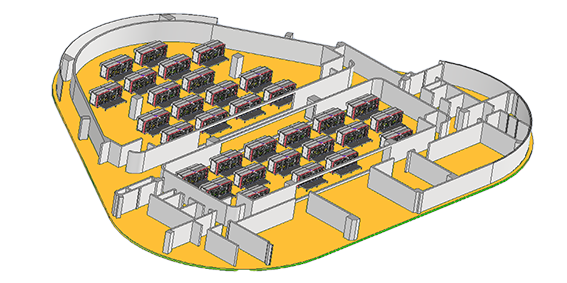
30kW Rig containing:
*DriveR Pulley.
*DriveN Pulley.
*6 off Idler Pulleys.
*A satellite unit can increase belt length capabilities, adding 5 more idler pulleys
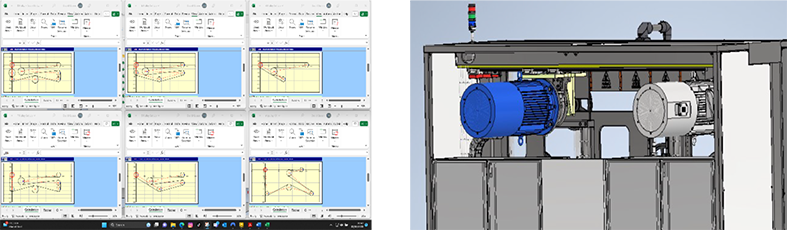
Department will have a fully inclusive IT system in control of:
*Test assignment.
*Product input.
*Pulley lifetime monitoring.
*Calibration.
*Real time data and photograph collection.
*Automated reporting (incl. identical testing of different manufacturers across multiple rigs).
*Authorized access is possible globally – Real time
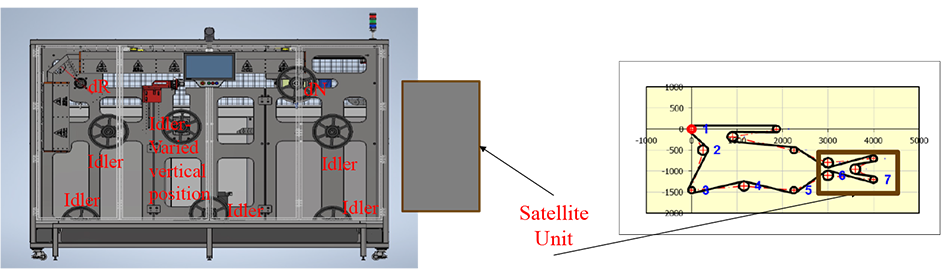
Rig advanced features are as follows:
*Ability to fit a large range of belt lengths (800mm to 16000mm) and types (Wrapped V-Belt, Cogged V-Belt, Ribbed Belt, Variable Speed Belt, Banded Belt, as well as Timing Belt).
*Belt life is greatly affected by temperature - our rig will capture life time behavior of:
- Working temperature changes due to friction.
- Belt life and performance under incremental temperature change.
- Slip on Driver pulley versus Driven pulley as slippage causes heat variations in the belt.
*Our rig will test and capture the physical changes of the belt under the following conditions:
- Effect of back bending on belt due to bending around back idlers.
- Wear of belt through dynamic micro photography.
- Dynamic tension loss.
- Real time belt measurement via infrared lasers.
- Early failure detection, vibration sensor paired with temperature change - facilitating better diagnosis of belt failure.
*Comparative testing (versus competition or others) through multiple rigs output from live reporting canl be linked on real time.
Data capture:
All data are saved for analysis using our integrated AI - Able to investigate and determine the root cause of failures and determine which of the belt elements will need improvements, updates, and/or changes. Able to further develop new generation programs based on our AI further data analysis and formulations.